Injection molds require regular cleaning, lubrication, and damage assessment. This ensures consistent production and extends the lifespan of the tooling. Click the Plastic Injection Mold Repair Florida to learn more.
A structured maintenance process minimizes mental mistakes and improves troubleshooting skills. It also helps technicians prioritize repair options based on the severity of the damage and expected mold lifespan.
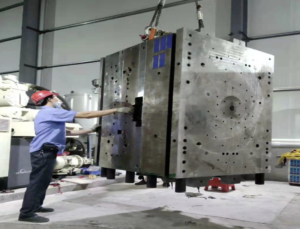
Grinding is a crucial step in turning raw materials into precision products. It helps achieve tight tolerances and superior surface finishes, and it’s especially important in the plastic injection molding industry.
While machining and hard gating have largely replaced grinding in many aspects of injection molding production, this process remains an integral part of the manufacturing workflow. After all, virtually every injection mold component must be ground. This includes the base of the mold, sprue bushings, leader pins and bushings, core and cavity plates, inserts, lifters, gibs, wear plates, ejector pins and core pin bushings, date wheels and other components.
Regular maintenance can help extend the life of injection molds, improve product quality and increase productivity. Taking the time to address common problems like misalignment, thermal cycling and degradation of cooling channels can significantly reduce the need for costly repairs.
The frequency of mold changes and setups can also have a direct impact on a plastic mold’s lifespan. Frequent changes can cause physical damage and alignment issues, which reduces a mold’s effective lifespan by around 20%. Embracing a standardized setup process and training staff to handle molds with care can minimize the risk of these kinds of problems.
Injection molds need to be carefully maintained in order to produce high-quality parts and avoid expensive repairs. However, even the most meticulous inspection and maintenance can sometimes lead to a need for mold repair. It’s important to recognize the signs of a damaged or worn injection mold so that you can take action promptly.
Flash is one of the most common indicators that your injection mold needs to be repaired or replaced. Flash occurs when the injection mold doesn’t seal properly, which leads to a gap or vent in the finished part. It may be caused by misalignment, excessive pressure or temperature, or a change in resin blend.
A poorly functioning injection mold will produce parts that are inconsistent in quality and appearance, resulting in costly returns and unplanned downtime. To prevent these problems, implement regular maintenance, including welding and grinding, to keep your injection molds in good condition. In addition, installing a chemical fume control system can help reduce respiratory hazards and make cleaning and repairing the molds much safer.
Machining
Injection molds are costly investments that must be carefully maintained to ensure high production rates and quality results. Over time, wear and tear can lead to mold issues that impact the quality of finished products and slow down productivity. Detecting these signs early can help manufacturers identify the best course of action for addressing injection mold repair and replacement needs to minimize downtime and maintain production rates.
Often, the first sign of injection mold problems is surface delamination or cracking. This type of damage is caused by high stress concentrations, temperature fluctuations, or poor quality materials and should be addressed as soon as possible to avoid further deterioration of the mold and the resulting production delays.
Another common indicator of injection mold damage is changes in the dimensions of the molded part, such as unexplained fluctuations in thickness or size. These changes are caused by wear and tear to critical elements of the mold, such as the cavity, core, or ejector pins. If these changes aren’t addressed, the mold could begin to produce parts that don’t meet specification requirements.
A systematic damage assessment process can help to prioritize repairs based on their impact on production, cost, and expected lifespan. This process should start with a visual inspection of the mold to identify any visible cracks, wear, or other damage. This can be followed by more detailed examinations using non-destructive testing methods such as ultrasonic testing, magnetic particle inspection, or dye penetrant testing.
Other indicators of injection mold wear include wavy patterns on the surfaces of finished parts. This is a result of pressure from the molten plastic as it pushes against the mold. In some cases, this can also be caused by insufficient cooling and poor mold closure.
Regular maintenance of injection molds can extend their lifespan and improve production efficiency by minimizing downtime due to unexpected mold-related issues. Well-maintained molds can also have consistent cycle times, which helps to ensure that production targets are met without compromising product quality. If you are experiencing production delays due to mold-related issues, it may be time to consider hiring a company to perform injection mold repair and revision services.
Welding
Injection molds need to be kept in good condition for production to run smoothly. This includes regular cleaning, lubrication, and a wear-and-tear assessment. Keeping detailed maintenance logs can help identify issues before they cause costly downtime and production delays.
Depending on the severity of the damage, several repair methods can be used. Surface grinding can smooth out any blemishes or scratches, while polishing and metalworking can address deeper problems. Welding is typically used to repair cracks or fractures in injection molds. This process can be tricky since it involves melting the base metal and forming oxide layers, which can lead to damage to the mold component.
To mitigate this, the injection mold needs to be prepared prior to welding by removing any contaminants and oxides. Then, a laser is used to precisely heat the area being repaired. This method minimizes the impact to surrounding areas and produces a high-quality weld. It is important to note that the weld will also show up in the finished product, so it must be blended properly.
Another common repair method is arc welding, which is used to repair larger holes or cracks in the injection mold. The arc welds are stronger and more precise than the laser welds, but they do create a HAZ (Heat affected zone) in the center of the weld. This isn’t ideal for precision plastic injection molding, but it can be an option in emergency situations when a production slowdown or shutdown may be unavoidable.
Finally, micro welding is used for smaller repairs in plastic injection molding. This process is similar to TIG welding, but uses a smaller filler wire and lower amperage settings to create a more precise weld. This method reduces the amount of machine or manual work required to take the mold back to net shape, and it is more versatile than standard TIG welding. However, it is important to note that micro welding still creates a HAZ in the center of the weld, which requires careful blending. Nonetheless, it is an excellent option for repairing small defects in plastic injection molding.
Refinishing
A refinishing process is used when the surface of the mold needs to be restored. The process removes the worn down surface, restoring the original surface of the mold. The refinishing process uses several tools, including a grinder, lapping machine, and polishing wheel. It also requires a large amount of energy, which can affect the environment.
The refinishing process uses high heat, which can lead to smoke, fumes, and toxic gases. These gases can cause a variety of health problems, including respiratory irritation and lung damage. They can also cause a number of other side effects, such as eye irritation and headaches. It is essential to take the necessary steps to protect workers from these hazardous substances.
Performing regular maintenance on injection molds can significantly extend their lifespan and reduce the need for costly repairs. This maintenance can include regularly cleaning and lubricating the injection mold, as well as scheduling inspections to identify issues early on. It is also important to store the molds in a controlled environment to prevent rust and degradation. Finally, ensuring that personnel are trained in proper handling and handling techniques can help to prolong the life of the mold.
The type of plastic material used in the injection molding process can also impact the duration of the mold’s lifespan. Certain materials require more frequent maintenance to reduce wear and tear due to higher temperatures or abrasive properties. Providing adequate rest periods between production cycles can also help to reduce thermal and mechanical stress on the mold, extending its effective lifespan.
One of the most common signs that an injection mold may be in need of repair is a change in the dimensions of finished products. This can be caused by wear and tear on the core, cavity, or ejection system. A loss of tolerance in these parts can lead to an increased number of defects and reduced productivity.
Effective maintenance of injection molds can dramatically increase their lifespan and improve productivity. By regularly cleaning and re-lubricating the molds, technicians can reduce the buildup of residues, which can cause a reduction in the efficiency of the mold and reduce its effective lifespan. Additionally, a structured sequence of maintenance procedures can reduce the number of mental mistakes that can cause costly errors and improve troubleshooting skills, which in turn can boost overall efficiency.