Foundation repair is essential for maintaining the integrity of any structure. Over time, soil shifts and environmental factors cause damage to foundations.
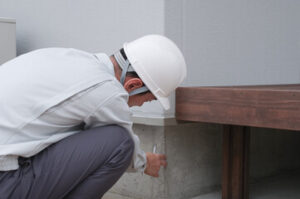
Cracks, uneven surfaces, and settling are common signs of foundation problems. Addressing these issues early prevents further structural damage and costly repairs. Visit Website to learn more.
Soil composition plays a major role in foundation stability. Expansive soil swells and contracts with moisture changes, leading to shifting foundations. Loose or poorly compacted soil causes uneven settling. Identifying soil type helps determine the best repair methods.
Moisture levels significantly impact foundation health. Excess moisture causes soil to expand and exert pressure on the foundation. Poor drainage leads to water pooling, weakening the foundation over time. Maintaining proper moisture balance prevents soil movement and foundation stress.
Temperature fluctuations affect foundation integrity. Freezing and thawing cycles cause soil to expand and contract. This movement creates stress on the foundation, leading to cracks and misalignment. Stabilizing soil temperature minimizes structural strain.
Tree roots pose a threat to foundation stability. Roots grow toward moisture sources and displace soil beneath the foundation. This creates voids and uneven pressure, resulting in foundation shifting. Removing problematic roots protects the foundation from damage.
Improper construction techniques lead to foundation issues. Inadequate footing depth and poor soil preparation weaken structural support. Using substandard materials reduces the foundation’s ability to withstand environmental changes. Professional construction practices improve long-term foundation health.
Cracks in the foundation signal structural weakness. Hairline cracks may seem minor but can widen over time. Diagonal or stair-step cracks indicate significant movement and stress. Early crack repair prevents further foundation shifting.
Foundation settlement causes uneven floors and misaligned walls. Soil erosion and poor compaction create voids beneath the foundation. These voids cause the foundation to sink and shift. Lifting and stabilizing the foundation restores structural alignment.
Water infiltration weakens foundation materials. Water seeps into cracks and pores, causing erosion and mold growth. Prolonged exposure to moisture deteriorates concrete and weakens support beams. Sealing cracks and improving drainage prevent water damage.
Poor drainage systems contribute to foundation instability. Downspouts and gutters that direct water toward the foundation increase soil saturation. Redirecting water flow reduces pressure on the foundation. Proper grading ensures that water drains away from the structure.
Foundation heaving results from soil expansion beneath the foundation. Expanding soil lifts portions of the foundation, causing cracks and misalignment. Installing root barriers and improving soil drainage reduces heaving. Stabilizing soil conditions prevents future upward movement.
Piers and pilings provide structural support for sinking foundations. These deep supports transfer the load to stable soil layers. Installing piers beneath the foundation prevents further settling. This method restores the foundation to its original position.
Helical piers are effective for stabilizing shifting foundations. These screw-like supports are driven into stable soil layers. The helical design provides resistance to movement. Helical piers offer long-term stability for weakened foundations.
Slab jacking raises sunken concrete slabs. This method involves injecting a cement-like mixture beneath the slab. The mixture fills voids and lifts the slab to its original level. Slab jacking is a cost-effective solution for minor foundation settlement.
Foam injection is a modern alternative to slab jacking. Expanding polyurethane foam fills voids and lifts the foundation. The lightweight nature of the foam reduces soil pressure. Foam injection provides fast and long-lasting foundation stabilization.
Steel push piers offer strong foundation support. These piers are driven into the ground until they reach stable soil. The weight of the structure is transferred to the piers. Steel piers prevent further settlement and improve foundation strength.
Wall anchors correct bowing and leaning walls. Anchors are installed into the surrounding soil and attached to the wall. Tightening the anchors gradually pulls the wall into alignment. This method strengthens weakened walls and prevents future movement.
Carbon fiber strips reinforce cracked and bowing walls. The lightweight and high-strength material resists tension. Installing carbon fiber strips prevents cracks from widening. This method offers a non-invasive solution for wall stabilization.
Underpinning strengthens and stabilizes weakened foundations. This process involves extending the foundation depth to reach stable soil. Concrete or steel supports are used to reinforce the foundation. Underpinning increases load-bearing capacity and prevents further settlement.
Epoxy and polyurethane injections seal foundation cracks. Epoxy provides structural reinforcement, while polyurethane blocks water intrusion. Injections fill deep cracks and restore the foundation’s integrity. This method prevents cracks from expanding and protects against moisture damage.
Mudjacking lifts uneven foundation slabs. This technique involves pumping a slurry beneath the slab. The slurry fills voids and raises the slab to an even level. Mudjacking restores structural alignment and prevents trip hazards.
Basement waterproofing protects the foundation from moisture damage. Interior and exterior waterproofing methods create barriers against water infiltration. Sump pumps and drainage systems remove excess water. Waterproofing strengthens foundation materials and reduces mold risk.
Foundation vents improve air circulation and reduce moisture buildup. Proper ventilation prevents mold growth and wood rot. Sealing foundation vents during wet seasons blocks moisture entry. Managing ventilation levels maintains a balanced moisture environment.
Foundation bracing reinforces weak or unstable foundations. Steel or wood braces are installed to support foundation walls. Bracing distributes structural load evenly. This method prevents further cracking and bowing.
Seismic retrofitting strengthens foundations against earthquakes. Installing anchor bolts and shear walls increases structural resistance to ground movement. Flexible connections reduce the impact of shifting soil. Seismic retrofitting protects structures from earthquake damage.
Perimeter drains direct water away from the foundation. Installing gravel-filled trenches with drainage pipes prevents soil saturation. Perimeter drains reduce hydrostatic pressure on foundation walls. This method prevents foundation cracking and erosion.
Moisture barriers protect the foundation from ground moisture. Plastic or fabric sheets are installed beneath the foundation. These barriers block moisture from seeping into concrete. Reducing moisture exposure strengthens foundation materials.
Void filling stabilizes shifting foundations. Foam or cement mixtures are injected into empty spaces beneath the foundation. Filling voids prevents further settlement. This method restores even weight distribution and strengthens the foundation.
Pressure grouting stabilizes loose soil beneath the foundation. High-pressure injection of grout fills gaps and compacts soil. This process increases soil density and load-bearing capacity. Pressure grouting prevents further soil shifting.
Hydraulic lifting raises settled foundations. Hydraulic jacks are used to lift the foundation evenly. Steel or concrete supports are installed to maintain position. Hydraulic lifting restores the foundation’s original height and alignment.
Soil stabilization improves foundation support. Adding stabilizing agents to soil increases strength and reduces expansion. Chemical or mechanical stabilization methods enhance soil composition. Stable soil prevents uneven settling and foundation stress.
Pier and beam repair strengthens raised foundations. Adjusting and reinforcing beams corrects sagging and uneven surfaces. Replacing damaged piers improves structural balance. Pier and beam repair enhances foundation durability.
Foundation insulation reduces temperature fluctuations. Insulating foundation walls prevents heat loss and condensation. Proper insulation protects concrete from moisture damage. This method improves foundation lifespan and structural stability.
Foundation repair protects the entire structure. Addressing cracks and shifts early prevents further damage. Professional evaluation identifies hidden issues. Regular maintenance ensures long-term foundation stability and structural safety.